Acoplamento para Redutor: Entenda a Importância
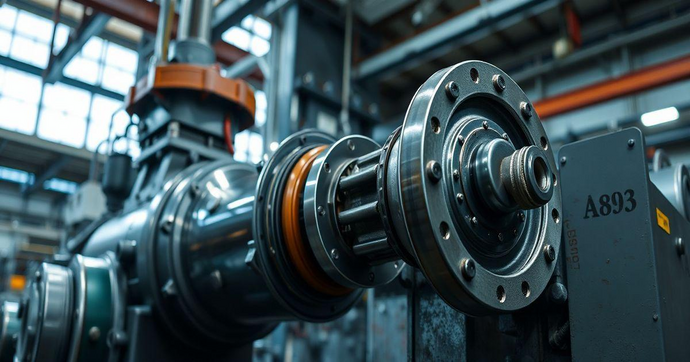
Por: Rodrigo - 25 de Dezembro de 2024
Acoplamento para redutor é um componente fundamental em sistemas de transmissão de potência, garantindo eficiência e desempenho. Neste artigo, iremos explorar os diferentes tipos de acoplamentos, como escolher o modelo ideal para suas necessidades e a importância da manutenção adequada. Continue lendo para descobrir como esses dispositivos podem melhorar o funcionamento das suas máquinas e evitar problemas operacionais.
O que é um acoplamento para redutor
Um acoplamento para redutor é um componente mechanical utilizado para conectar duas partes de um sistema de transmissão de potência, especialmente entre um motor e um redutor de velocidade. Ele tem a função principal de transmitir torque e movimento rotativo enquanto permite o alinhamento e a acomodação de pequenas descontinuidades. O uso de acoplamentos é vital para garantir a eficiência e a durabilidade de equipamentos industriais e maquinários em geral.
Os acoplamentos são projetados para suportar variações de ângulo, como desvios de alinhamento entre eixos, e ainda permitir a absorção de choques e vibrações. A escolha do tipo adequado de acoplamento para redutor pode ter um grande impacto na performance operacional, aumentando a vida útil dos componentes e reduzindo a necessidade de manutenção frequente.
Existem diferentes tipos de acoplamentos disponíveis no mercado, cada um com suas próprias características e aplicações específicas. Alguns exemplos incluem o acoplamento bipartido , que é amplamente utilizado por sua flexibilidade e facilidade de manutenção. Outro tipo comum é o acoplamento rígido, que, embora ofereça alta capacidade de transmissão, não tolera desvios de alinhamento.
Os acoplamentos para redutores podem ser classificados em várias categorias, como flexíveis e rígidos. Os flexíveis, por exemplo, são projetados para acomodar desalinhamentos angulares e axiais, permitindo assim um funcionamento suave e evitando o desgaste excessivo nos componentes acoplados. Isso é especialmente importante em aplicações onde a precisão e eficiência são cruciais.
Uma das principais funções do acoplamento para redutor é transmitir potência de maneira eficiente. Durante o funcionamento, o motor gera torque, que precisa ser transmitido ao redutor para que a energia mecânica seja convertida em movimento útil. Se o acoplamento não for adequado, isso pode resultar em perda de potência, aumento de vibrações e desgaste precoce dos componentes.
O material com o qual o acoplamento é fabricado também influencia suas características de desempenho. Os acoplamentos podem ser feitos de aço, alumínio ou materiais poliméricos, cada um oferecendo vantagens e desvantagens. Por exemplo, os acoplamentos de aço são duráveis e resistentes à carga, enquanto os de materiais poliméricos podem oferecer maior flexibilidade e redução de peso.
Para maximizar a eficiência dos acoplamentos para redutores, é importante levar em consideração fatores como a tensão, a velocidade, a temperatura de operação e o ambiente em que o sistema será utilizado. Todos esses elementos afetam a seleção e o desempenho do acoplamento. Um diagnóstico apropriado no momento da escolha do acoplamento pode evitar problemas operacionais futuros, como quebras inesperadas e longas paradas de produção.
A manutenção também desempenha um papel essencial na eficácia dos acoplamentos para redutores. Exames regulares e a aplicação de lubrificantes apropriados podem aumentar significativamente a vida útil do acoplamento. A verificação de sinais de desgaste, como folgas excessivas ou quebras, deve ser parte do procedimento padrão de manutenção preventiva. Tomar essas medidas ajuda a evitar falhas súbitas e a garantir que o sistema funcione eficientemente.
Além disso, a instalação correta do acoplamento é fundamental. Um alinhamento inadequado durante a instalação pode levar a falhas prematuras e ao aumento do desgaste de outros componentes do sistema. Portanto, é aconselhável que a instalação seja realizada por profissionais treinados que compreendam as especificidades daquela aplicação.
Por fim, a escolha do acoplamento para redutor é uma decisão técnica que pode afetar diretamente a operação de um sistema. Um entendimento claro sobre as funções e tipos de acoplamentos disponíveis pode fazer toda a diferença na eficiência e na durabilidade de um sistema de transmissão de potência. Considerando os fatores mencionados, os operadores podem garantir que seus sistemas sejam mais confiáveis e econômicos a longo prazo.
Tipos de acoplamentos para redutor
Os acoplamentos para redutor são componentes essenciais em sistemas de transmissão de potência, e sua seleção correta pode ter um impacto significativo na eficiência do maquinário. Existem vários tipos de acoplamentos, cada um projetado para atender a necessidades específicas de conexão, acomodação de desalinhamentos e transmissão de torque. Neste artigo, iremos explorar os principais tipos de acoplamentos para redutores e suas características.
O primeiro tipo a ser mencionado é o acoplamento rígido. Este tipo não apresenta flexibilidade e é ideal para aplicações onde o alinhamento entre os eixos é preciso. O acoplamento rígido é frequentemente utilizado em situações onde a precisão é fundamental, pois minimiza a perda de torque entre as partes conectadas. No entanto, sua falta de flexibilidade significa que ele não pode acomodar desalinhamentos, o que pode levar a desgastes e falhas se não for instalado corretamente.
Outro tipo comum é o acoplamento flexível, que permite a compensação de desalinhamentos angulares e axiais. Este tipo é amplamente utilizado em aplicações onde a movimentação e vibrações são inevitáveis, proporcionando maior proteção aos componentes conectados. Os acoplamentos flexíveis podem ser encontrados em várias formas, incluindo discos de elastômero e molas que permitem o movimento entre as peças. O acoplamento elástico de pinos , por exemplo, é um tipo de acoplamento flexível que se destaca pela sua capacidade de absorver choques e vibrações, aumentando a durabilidade do sistema.
Outro tipo importante é o acoplamento de alta flexibilidade. Este acoplamento é projetado para suportar grandes desalinhamentos e vibrações, tornando-se ideal para aplicações industriais pesadas. Com sua capacidade de deformação, o acoplamento de alta flexibilidade proporciona uma operação tranquila, reduzindo o estresse em outras partes do sistema. É muito utilizado em indústrias de mineração e construção, onde os níveis de estresse são mais elevados.
Os acoplamentos de discos também merecem destaque. Eles são compostos por discos de metal que se conectam entre si, permitindo uma transmissão de torque altamente eficiente. Esses acoplamentos são caracterizados pela sua rigidez e precisão, tornando-os ideais para sistemas que exigem alta performance. De maneira geral, os acoplamentos de discos são menos flexíveis do que os acoplamentos elastoméricos, mas são mais eficazes em condições onde a precisão é crucial.
O acoplamento de engrenagens é outro tipo frequentemente utilizado. Esse acoplamento utiliza engrenagens para conectar dois eixos, garantindo que o torque seja transmitido de forma eficiente e sem perda de energia. O acoplamento de engrenagens é capaz de acomodar alguns desalinhamentos, embora não seja tão flexível quanto os acoplamentos elastoméricos. No entanto, sua capacidade de transmissão de torque em altas velocidades o torna uma escolha popular em aplicações industriais.
Além desses, há os acoplamentos de furo cônico. Eles são projetados para fornecer uma conexão firme entre as peças através de um ajuste cônico. Essa estrutura permite uma instalação mais fácil e rápida, além de oferecer um pouco de flexibilidade para desalineamentos menores. Os acoplamentos de furo cônico são frequentemente utilizados em aplicações onde a rapidez na instalação e a manutenção são fatores que precisam ser considerados.
Os acoplamentos de lâmina também são uma opção viável. Estes acoplamentos utilizam lâminas de metal para conectar eixos e são conhecidos por sua capacidade de absorver choques e vibrações. A principal vantagem do acoplamento de lâmina é a sua leveza e a capacidade de suportar altas forças de tração, o que o torna ideal para aplicações em alta velocidade e com um alto nível de desempenho.
Por fim, temos os acoplamentos hidráulicos, que operam com fluídos para fornecer uma conexão entre eixos. Eles são particularmente úteis em aplicações onde é necessário transmitir grandes quantidades de energia com segurança. Os acoplamentos hidráulicos podem acomodar desalinhamentos maiores do que outros tipos, e são frequentemente encontrados em máquinas pesadas, onde a capacidade de suportar altas cargas é essencial.
Entender os diferentes tipos de acoplamentos disponíveis no mercado é fundamental para garantir a eficiência e a durabilidade do sistema de redutor. A seleção do acoplamento adequado não só evita desgastes prematuros, mas também melhora o desempenho geral do maquinário. Seja para aplicações simples ou complexas, existe um acoplamento que atenderá às necessidades específicas de cada sistema.
Como escolher o acoplamento ideal
A escolha do acoplamento ideal é uma decisão crítica para garantir a eficiência e a durabilidade de sistemas de transmissão de potência. Um acoplamento adequado não só assegura que a energia seja transmitida eficientemente entre as partes conectadas, mas também protege o maquinário de desgaste excessivo e falhas mecânicas. Para fazer essa escolha de forma informada, devem ser considerados diversos fatores.
O primeiro passo na escolha do acoplamento ideal é entender as necessidades específicas da sua aplicação. Cada tipo de acoplamento apresenta características distintas que podem torná-lo mais ou menos adequado para situações específicas. Por exemplo, se o sistema exigir um alto grau de flexibilidade para lidar com desalinhamentos, você pode optar por Acoplamento De Pino ou por um acoplamento elastomérico. Por outro lado, se a precisão for crucial, um acoplamento rígido pode ser a melhor escolha.
Outro fator importante é o torque que será transmitido pelo acoplamento. Cada tipo de acoplamento suporta um limite máximo de torque, que deve ser considerado para evitar falhas. Calcule o torque máximo que seu motor pode gerar e escolha um acoplamento que suporte essa carga, além de um fator de segurança adequado. A regra geral é sempre escolher um acoplamento que tenha uma capacidade de carga superior à que será exigida na operação.
Além do torque, a velocidade de operação também é um critério fundamental. Diferentes acoplamentos têm limites diferentes para a velocidade de rotação, e escolher um que não suporta a velocidade máxima pode resultar em danos. Verifique as especificações do acoplamento e compare com as velocidades de operação do seu sistema. Um acoplamento de alta velocidade deve ser considerado em aplicações que operam com rotação acelerada.
Outro aspecto a ser analisado é o alinhamento dos eixos. Se o sistema tiver um alinhamento muito precisão, um acoplamento rígido pode ser suficiente. No entanto, se houver alguma possibilidade de desalinhamento, um acoplamento flexível será mais adequado. Isso é particularmente relevante em condições de operação onde a vibração ou movimento podem causar desalinhamentos inesperados. Por isso, medir o nível de desalinhamento esperado ajudará a determinar o tipo de acoplamento necessário.
A especificidade do ambiente também pode influenciar a escolha do acoplamento ideal. Condições extremas de temperatura, umidade ou exposição a produtos químicos podem danificar certos tipos de acoplamentos. Por exemplo, em ambientes industriais extremamente quentes ou frios, materiais que não suportam essas condições podem falhar rapidamente. Certifique-se de que o acoplamento escolhido seja feito de material adequado que possa suportar as condições ambientais da sua aplicação.
Outro ponto crucial é a manutenção. Alguns tipos de acoplamentos exigem mais manutenção do que outros. Acoplamentos com materiais elastoméricos, por exemplo, podem necessitar de uma substituição mais frequente em comparação com acoplamentos metálicos que são mais robustos. Avalie a disponibilidade de manutenção e o acesso ao acoplamento em caso de necessidade. Um sistema que é de fácil manutenção pode economizar tempo e dinheiro a longo prazo.
A instalação é outro aspecto a ser considerado. Acoplamentos que são simples de instalar podem economizar tempo e custos trabalhistas. A instalação inadequada de um acoplamento pode resultar em falhas futuras e redução da vida útil do componente. Acoplamentos que têm recursos de alinhamento simplificados podem ser benéficos em um ambiente onde a precisão de instalação é um desafio.
Por fim, consulte sempre os fabricantes e especialistas para obter recomendações. Profissionais da área muitas vezes têm experiência e conhecimento que podem ajudar a identificar o acoplamento mais adequado para suas necessidades específicas. Eles podem oferecer insights sobre as últimas inovações no mercado e sobre como diferentes acoplamentos se comportam em diferentes condições.
Em resumo, escolher o acoplamento ideal envolve uma avaliação cuidadosa de diversos fatores, incluindo as necessidades específicas da aplicação, torque e velocidade, alinhamento e ambiente operacional, manutenção e instalação. Um acoplamento bem escolhido não só garantirá o funcionamento eficiente do sistema, mas também aumentará a durabilidade e reduzirá a necessidade de intervenções frequentes, resultando em maior economia a longo prazo. Portanto, invista o tempo necessário nesta decisão e siga as diretrizes mencionadas para obter o melhor resultado possível.
Vantagens do uso de acoplamentos em redutores
O uso de acoplamentos em redutores é crucial para garantir a eficiência e a durabilidade de equipamentos em diversas aplicações industriais. Esses componentes desempenham um papel vital na transmissão de potência e movimento rotativo, permitindo que motores e redutores trabalhem de forma sinérgica. Vamos explorar as principais vantagens de utilizar acoplamentos em redutores e como eles podem beneficiar seu sistema.
Uma das principais vantagens dos acoplamentos é a capacidade de compensar desalinhamentos entre eixos. Em muitas aplicações, uma leve imprecisão no alinhamento dos eixos pode ocorrer, resultando em vibrações e desgaste excessivo em componentes. Um acoplamento flexível pode acomodar esses desalinhamentos, evitando danos e prolongando a vida útil do redutor e do motor. Isso é especialmente relevante em sistemas que operam em ambientes vibratórios ou que podem sofrer variações na montagem ao longo do tempo.
Outra vantagem importante é a absorção de choques e vibrações. Durante a operação, máquinas e equipamentos podem estar sujeitos a cargas dinâmicas que resultam em picos de pressão e forças inesperadas. Os acoplamentos têm a capacidade de amortecer esses impactos, protegendo o motor e o redutor de danos potenciais. Além disso, ao minimizar as vibrações, os acoplamentos ajudam a garantir um funcionamento mais suave do sistema, o que é crucial para aplicações que exigem alta precisão.
A redução de desgaste e manutenção é outro benefício significativo que os acoplamentos oferecem. Ao criar uma interface entre o motor e o redutor que pode acomodar desalinhamentos e choques, os acoplamentos reduzem o desgaste em componentes críticos. Isso significa que os operadores podem esperar intervalos de manutenção mais longos e um menor custo de reparo e substituição de peças. Por exemplo, acoplamentos como o Acoplamento omega são projetados para maximizar a durabilidade, permitindo um funcionamento eficaz em uma variedade de condições de operação.
Os acoplamentos também podem ajudar a melhorar a eficiência energética do sistema. Um acoplamento adequado minimiza a perda de potência durante a transmissão de torque, o que significa que mais energia é convertida em movimento útil. Essa eficiência é particularmente importante em aplicações industriais, onde o custo da energia é significativo. Com menos energia desperdiçada em forma de calor ou vibrações, os sistemas podem operar de maneira mais custo-efetiva.
A instalação e remoção de acoplamentos são geralmente rápidas e fáceis, o que proporciona um benefício adicional em termos de tempo e custo. Muitos acoplamentos modernos são projetados para permitir uma instalação simples, reduzindo a necessidade de equipamentos especiais ou habilidades especializadas. Essa facilidade de instalação garante que, mesmo em testes de manutenção ou reparo, o tempo de inatividade do sistema seja minimizado, aumentando assim a produtividade geral.
Além das vantagens práticas de desempenho, os acoplamentos também contribuem para um ambiente operacional mais seguro. Ao proteger motores e redutores contra danos causados por desalinhamentos ou picos de carga, eles minimizam o risco de falhas mecânicas que podem resultar em acidentes no chão de fábrica. Essa proteção é vital, não apenas para a integridade do equipamento, mas também para a segurança dos operadores e técnicos que trabalham nas proximidades das máquinas.
Outro aspecto positivo do uso de acoplamentos pode ser observado no aumento da versatilidade das aplicações. Com uma ampla gama de tipos de acoplamentos disponíveis, os operadores podem escolher aqueles que melhor atendem às necessidades específicas de suas operações. Isso permite adaptabilidade em diversas situações e a capacidade de trocar componentes conforme mudanças nos requisitos de produção.
A correção do alinhamento também é facilitada com o uso de acoplamentos. Alguns modelos de acoplamentos vêm com características específicas que permitem ajustes fáceis para compensar quaisquer desalinhamentos que possam ocorrer durante a instalação e durante o funcionamento. Isso garante que os sistemas operem em níveis de eficiência ideais, mantendo a qualidade de produção e evitando problemas associados a alinhamentos inadequados.
Por último, os acoplamentos também desempenham um papel importante na redução de ruídos operacionais. Muitas vezes, equipamentos que operam sem um acoplamento adequado podem gerar ruídos excessivos, que não apenas são indesejáveis, mas também podem ser um sinal de problemas mecânicos iminentes. Os acoplamentos ajudam a mitigar esses ruídos, contribuindo para ambientes de trabalho mais seguros e confortáveis.
Em suma, as vantagens do uso de acoplamentos em redutores são vastas e abrangem aspectos de eficiência, durabilidade, manutenção e segurança. A escolha correta do acoplamento pode resultar em operações mais suaves, redução de custos operacionais e uma vida útil prolongada para o equipamento. Portanto, considerar o uso de acoplamentos em suas aplicações industriais não é apenas uma escolha técnica, mas uma decisão estratégica que pode resultar em um desempenho significativamente melhorado em suas operações.
Instalação de acoplamentos para redutor
A instalação de acoplamentos para redutores é uma etapa crucial que pode impactar diretamente a eficiência e a durabilidade do sistema de transmissão de potência. Uma instalação inadequada pode levar a problemas sérios, como desgaste prematuro, falhas mecânicas e até mesmo acidentes operacionais. Portanto, é fundamental prestar atenção a cada detalhe durante esse processo. Neste artigo, discutiremos as melhores práticas para a instalação de acoplamentos em redutores, garantindo um desempenho ideal!
O primeiro passo para uma instalação bem-sucedida é a escolha do acoplamento apropriado. Antes de começar a instalação, é necessário entender as especificações do sistema, incluindo o tipo de redutor e motor utilizados, o torque e a velocidade operacionais, além das condições ambientais. A escolha correta do acoplamento que atenda a essas especificações assegurará que a instalação será mais tranquila e eficaz.
Uma vez escolhido o acoplamento, o próximo passo é a preparação dos eixos que serão conectados. Antes de iniciar a instalação, é importante limpar a superfície dos eixos, garantindo que não haja resíduos de óleo, poeira ou sujeira que possam interferir na conexão. Além disso, deve-se inspecionar os eixos em busca de danos ou desgaste. Qualquer falha nos eixos pode comprometer o desempenho do acoplamento.
O alinhamento dos eixos é um dos aspectos mais críticos na instalação de acoplamentos. Um alinhamento inadequado pode causar estresse excessivo no acoplamento, levando a desgastes prematuros e falhas. Para garantir um bom alinhamento, utilize ferramentas adequadas, como ferramentas de alinhamento a laser ou de direcionalidade, que trazem um alto nível de precisão. Ajuste os eixos até que eles estejam alinhados dentro das tolerâncias especificadas pelo fabricante do acoplamento.
Depois que os eixos estiverem alinhados, é hora de posicionar o acoplamento. Certifique-se de que o acoplamento esteja montado corretamente, seguindo as instruções do fabricante. Geralmente, o acoplamento deve ser instalado usando um movimento uniforme e firme, evitando choques que possam danificá-lo. Evite forçar o acoplamento, pois isso pode resultar em danos ao próprio componente e à estrutura do redutor.
Após a instalação inicial, é essencial realizar uma verificação de folgas e ajustes. Utilize instrumentos de medição para garantir que as folgas estejam dentro das especificações. Se for necessário, faça ajustes adicionais no alinhamento para minimizar a folga. Uma transmissão suave de torque depende de um ajuste adequado do acoplamento. Qualquer folga excessiva poderá causar vibrações indesejadas e ruídos durante a operação.
O torque de aperto também é um fator vital no processo de instalação. Seguir as especificações do fabricante quanto ao torque dos parafusos ou fixadores que prendem o acoplamento é fundamental. Aperte cada parafuso de maneira uniforme, em um padrão cruzado, para garantir uma distribuição uniforme da força. É importante realizar essa etapa com cuidado, pois um torque excessivo pode causar danos ao acoplamento, enquanto um torque insuficiente pode resultar em folgas indesejadas.
Após concluir a instalação, sempre faça uma revisão final antes de colocar o sistema em operação. Verifique se todos os parafusos estão devidamente apertados, se não há folgas excessivas e se o alinhamento dos eixos é adequado. Essa revisão final pode prevenir problemas que poderiam ocorrer durante a operação e economizar tempo e recursos no futuro.
É recomendável realizar um teste operacional após a instalação. Isso envolve ligar o sistema e monitorar a operação inicial do acoplamento. Preste atenção a qualquer ruído excessivo, vibrações ou superaquecimento. Se algum desses fenômenos ocorrer, pode ser necessário realizar ajustes ou até mesmo reconsiderar a instalação. A observação constante durante os primeiros dias de funcionamento pode fornecer informações úteis sobre o desempenho do acoplamento.
Por último, nunca subestime a importância da documentação. Manter registros adequados sobre a instalação, incluindo datas, métodos utilizados, e verificação de alinhamento e folgas, pode ajudar na manutenção futura. Muitas vezes, documentos de instalação são requisitos fundamentais para auditorias e conformidade em ambientes industriais.
Em resumo, a instalação de acoplamentos para redutores deve ser realizada com atenção a cada detalhe, incluindo a escolha do modelo adequado, limpeza dos eixos, alinhamento preciso e verificação de tolérance. Adoptar uma abordagem sistemática e cuidadosa assegurará o funcionamento ideal do sistema, aumentando sua eficiência e prolongando a vida útil dos componentes. Um trabalho bem feito desde a instalação irá resultar em operações mais suaves, eficientes e seguras.
Manutenção de acoplamentos: Dicas importantes
A manutenção de acoplamentos é um aspecto essencial para garantir a eficiência e a durabilidade de sistemas de transmissão de potência em diversos ambientes industriais. Muitas vezes, é fácil esquecer que esses componentes estão sujeitos a desgaste e devem ser monitorados e mantidos regularmente. Aqui, discutiremos dicas importantes para a manutenção de acoplamentos, assegurando seu funcionamento ideal e evitando falhas que podem resultar em paradas não planejadas ou custos elevados de reparo.
Uma das principais práticas recomendadas é realizar inspeções regulares. A frequência das inspeções pode variar dependendo das condições operacionais, mas como regra geral, recomenda-se fazer uma verificação a cada 1000 horas de operação ou a cada seis meses, o que ocorrer primeiro. Durante essas inspeções, você deve procurar sinais de desgaste, como rachaduras, deformações ou folgas excessivas no acoplamento. Qualquer anomalia observada deve ser tratada imediatamente para evitar falhas mais sérias.
Além das inspeções visuais, é importante monitorar as vibrações do sistema. Vibrações excessivas podem indicar problemas de alinhamento ou desgaste nos acoplamentos. Utilizar ferramentas de monitoramento de vibração pode ajudar a identificar esses problemas antes que se tornem críticos. A análise de vibração pode fornecer dados valiosos, permitindo que os técnicos tomem medidas corretivas antes que uma falha ocorra.
Outro aspecto crítico da manutenção é a lubrificação adequada. Muitos acoplamentos requerem a aplicação regular de lubrificantes para garantir o funcionamento suave e eficiente. Verifique as especificações do fabricante quanto ao tipo de lubrificante a ser utilizado e a frequência de aplicação. Lubrificantes inadequados ou insuficientes podem causar fricção excessiva, levando ao superaquecimento e falhas no acoplamento. Nos casos em que o acoplamento possui selos, também é importante verificar a integridade desses selos para evitar vazamentos de lubrificante.
A limpeza dos acoplamentos é outra etapa importante na manutenção. Poeira, sujeira e outras impurezas podem se acumular ao longo do tempo e prejudicar o funcionamento do acoplamento. Faça a limpeza regularmente, utilizando produtos adequados e evitando substâncias químicas que possam danificar os materiais do acoplamento. A limpeza deve ser feita com cuidado para garantir que nenhum resíduo permaneça nas superfícies de contato.
O alinhamento deve também ser monitorado. Com o uso contínuo, é possível que um acoplamento que inicialmente estava bem alinhado comece a apresentar algum grau de desalinhamento devido a vibrações ou mudanças térmicas. Verifique o alinhamento a cada manutenção e faça os ajustes necessários. O alinhamento adequado não só minimiza o desgaste do acoplamento, mas também melhora a eficiência da transmissão de potência.
Outras práticas recomendadas incluem a verificação do torque de aperto dos parafusos de fixação. Os parafusos podem se afrouxar com o tempo devido a vibrações, e um aperto inadequado pode resultar em folgas indesejadas. Inspecione o torque dos parafusos periodicamente e siga as especificações fornecidas pelo fabricante do acoplamento. Utilize uma chave de torque para garantir que os parafusos estejam devidamente apertados.
Além disso, estar atento à temperatura de operação pode fornecer pistas sobre a saúde do acoplamento. Temperaturas elevadas podem indicar problemas de lubrificação, desalinhamento ou outros defeitos mecânicos. Instalar sensores de temperatura em áreas críticas pode ajudar a monitorar as condições operacionais e detectar problemas antes que eles se agravem.
Por último, a troca programada de acoplamentos deve ser considerada. Mesmo que um acoplamento esteja operando aparentemente bem, ele pode estar se aproximando do fim de sua vida útil, especialmente em aplicações exigentes. Developing a schedule for replacement intervals based on usage, wear and manufacturer guidelines can help prevent unexpected failures. Keep records of repairs and parts replacements for future reference and planning, allowing for a more proactive approach to maintenance.
Em resumo, a manutenção de acoplamentos envolve uma série de práticas que, quando seguidas regularmente, podem garantir o desempenho ideal desses componentes e a confiabilidade do sistema de transmissão de potência. Seja através de inspeções visuais, monitoramento de vibrações, lubrificação adequada ou troca programada, cada etapa desempenha um papel crucial na prevenção de problemas e na maximização da vida útil do acoplamento. Com um plano de manutenção abrangente, as empresas podem evitar falhas dispendiosas e manter operações contínuas e eficientes.
Aplicações práticas dos acoplamentos em redutores
Os acoplamentos desempenham um papel essencial em diversas aplicações industriais, conectando motores e redutores de maneira a garantir a transmissão eficiente de potência. A versatilidade e a eficácia desses componentes são fundamentais em várias áreas, desde a fabricação até a automação, e sua adequada aplicação pode resultar em sistemas de alta performance e operação suave. Vamos explorar as aplicações práticas dos acoplamentos em redutores e como eles contribuem para a eficiência e longevidade dos sistemas industriais.
Uma das aplicações mais comuns dos acoplamentos em redutores é em sistemas de transporte, como esteiras e correias transportadoras. Nesses sistemas, os acoplamentos garantem que a potência gerada por motores elétricos seja transmitida de forma eficiente a redutores, que por sua vez ajustam a velocidade do movimento. Isso é crucial em processos de mineração, onde materiais pesados são transportados continuamente. Os acoplamentos ajudam a garantir que a carga seja transferida suavemente, minimizando o desgaste e aumentando a confiabilidade do sistema.
Além dos sistemas de transporte, os acoplamentos são amplamente utilizados em equipamentos de processamento, como moinhos, britadores e mixers. Em aplicações como essas, a transmissão de torque preciso é fundamental para garantir uma operação eficiente e segura. Por exemplo, em um moinho de moagem, o acoplamento conecta o motor ao redutor e precisa suportar forças consideráveis durante a operação. Um acoplamento adequado não apenas transmite a potência de forma eficaz, mas também absorve choques e vibrações, protegendo os componentes críticos do equipamento.
Os acoplamentos também têm um papel fundamental em sistemas de bombeamento. Em sistemas onde bombas são acionadas por motores elétricos, os acoplamentos garantem a transmissão da energia necessária para mover fluidos, supersaturando a eficiência. A escolha correta do acoplamento pode afetar significativamente o desempenho da bomba, assim como sua capacidade de lidar com condições de operação extremas, como altas pressões e temperaturas. Por isso, a consideração cuidadosa durante o projeto e a instalação é fundamental para a operação contínua dessas aplicações.
Camas vibro-compactadoras, utilizadas na construção civil, também dependem de acoplamentos para seu funcionamento. O motor de vibração é conectado ao redutor através de um acoplamento, que não apenas transmite a potência, mas também permite a absorção de choques e vibrações. Isso garante que a compactação do solo seja realizada de forma eficiente, proporcionando uma base sólida para a construção. Os acoplamentos, nesse caso, ajudam a estender a vida útil dos componentes, minimizando os danos causados por vibrações excessivas.
Outra aplicação importante é nas máquinas-ferramentas da indústria metalúrgica. Essas máquinas frequentemente utilizam acoplamentos para conectar motores a sistemas de transmissão que movimentam ferramentas de corte com precisão. Os acoplamentos ajudam a garantir que a força aplicada pela ferramenta seja transmitida uniformemente, melhorando a qualidade do corte e reduzindo o desgaste da ferramenta. Em operações que exigem alta precisão, a escolha do acoplamento certo é fundamental para obter resultados consistentes.
A automação industrial também faz amplo uso de acoplamentos em redutores, especialmente em robôs industriais e sistemas de manuseio automático. Aqui, a precisão e a repetibilidade são vitais, e os acoplamentos ajudam a garantir que os motores de passo ou servomotores operem de forma sinérgica com os redutores. Isso resulta em movimentos suaves e controlados, essenciais para tarefas como montagem, soldagem e pintura. O desempenho confiável dessas operações depende da eficácia do acoplamento utilizado.
Além disso, os acoplamentos são utilizados em sistemas de ventilação e ar condicionado (HVAC). Neste caso, os ventiladores são frequentemente acionados por motores elétricos, e um acoplamento adequado é necessário para ajustar a rotação e criar a pressão necessária para o fluxo de ar adequado. Sistemas de HVAC que utilizam acoplamentos se beneficiam de operações silenciosas e eficientes, essenciais para ambientes de trabalho e conforto residencial.
Em aplicações de energia renovável, como turbinas eólicas, os acoplamentos desempenham um papel essencial na transmissão da potência gerada pelas lâminas da turbina para geradores que convertem essa energia em eletricidade. As variações de velocidade e torque requerem acoplamentos especialmente projetados para suportar condições de operação desafiadoras. Aqui, a confiabilidade dos acoplamentos é crucial, uma vez que a manutenção em turbinas eólicas é frequentemente complexa devido à localização remota das instalações.
Por último, mas não menos importante, os acoplamentos são usados em máquinas agrícolas, incluindo tratores e colheitadeiras. Nesse ambiente, a demanda por acoplamentos é alta, pois eles conectam motores e redutores que operam ferramentas e implementos que realizam tarefas diárias, como arar e semear. A resistência a impactos e a flexibilidade nos acoplamentos garantem que a operação agrícola seja eficiente e eficaz, mesmo em condições variadas e desafiadoras.
Em resumo, as aplicações práticas dos acoplamentos em redutores são vastas e variadas. Desde sistemas de transporte até equipamentos industriais, máquinas-ferramentas e automação, eles desempenham um papel crucial na eficiência operacional e na durabilidade dos sistemas. A escolha e a manutenção adequadas dos acoplamentos podem resultar em operações mais suaves e confiáveis em uma variedade de setores, exigindo atenção contínua para maximizar o desempenho e minimizar o desgaste. Ao considerar o papel vital dos acoplamentos, fica evidente que eles são componentes essenciais em qualquer sistema de transmissão de potência.
Erros comuns ao utilizar acoplamentos para redutor
A utilização de acoplamentos em redutores é essencial para garantir a eficiência e a durabilidade dos sistemas de transmissão de potência. No entanto, muitos operadores e profissionais enfrentam desafios e cometem erros que podem comprometer o desempenho e a vida útil desses componentes. Neste artigo, exploraremos os erros comuns ao usar acoplamentos para redutor e ofereceremos orientações sobre como evitá-los, garantindo assim um desempenho ideal.
Um dos erros mais frequentes é a escolha inadequada do acoplamento. Muitos profissionais não consideram as especificações do motor e do redutor, levando à seleção de um acoplamento que não atenderá às demandas operacionais. É fundamental que o acoplamento escolhido suporte o torque, a velocidade e as condições ambientais específicas do sistema. Ignorar essas especificações pode resultar em falhas mecânicas precoce e na necessidade de substituição frequente dos componentes.
Outro erro comum está relacionado ao alinhamento incorreto dos eixos. Um alinhamento impreciso pode causar desgaste excessivo e falhas prematuras no acoplamento, além de potenciais danos ao motor e redutor. Quando os eixos estão desalinhados, há um aumento na carga sobre o acoplamento, o que pode levar a vibrações excessivas e operações ineficientes. Utilizar ferramentas adequadas, como alinhadores a laser, pode ajudar a garantir que os eixos estejam corretamente alinhados durante a instalação.
A instalação inadequada do acoplamento também é uma armadilha frequente. Muitas vezes, os operadores podem não seguir o procedimento correto ao instalar o acoplamento, o que resulta em uma instalação mal executada. Isso pode incluir o uso de força excessiva ao apertar os parafusos, o que pode danificar o componente e comprometer sua operação. Também é importante garantir que não haja objetos estranhos ou resíduos entre as superfícies de contato do acoplamento e os eixos, que podem afetar a transmissão de torque.
Além disso, ignorar as recomendações do fabricante em relação à manutenção e aos períodos de inspeção é um erro que pode ter consequências graves. Muitos operadores não realizam verificações regulares dos acoplamentos, falhando em detectar sinais de desgaste ou danos que poderiam ser facilmente reparados. A falta de manutenção pode levar a falhas catastróficas e, consequentemente, a custos elevados de reparo e paralisações não programadas. Portanto, é fundamental seguir as diretrizes de manutenção estabelecidas pelo fabricante para garantir um desempenho ideal ao longo da vida útil do acoplamento.
Outra questão comum é a falta de lubrificação adequada. Muitos acoplamentos requerem lubrificação para funcionar de maneira eficiente, e a ausência dessa manutenção pode levar a atrito excessivo e superaquecimento. Um lubrificante inadequado ou a falta de lubrificação podem resultar em falhas prematuras do acoplamento e dos componentes conectados. É importante seguir as recomendações do fabricante em relação ao tipo e à frequência da lubrificação, garantindo que o acoplamento funcione dentro das condições ideais.
A temperatura de operação é também um fator crucial a ser considerado, e muitos operadores negligenciam esse aspecto. Altas temperaturas podem afetar a eficiência do acoplamento, reduzir a eficácia da lubrificação e, em última análise, causar danos. Monitorar continuamente a temperatura de operação do sistema é essencial para evitar sobrecargas e falhas. Implementar sistemas de monitoramento pode fornecer informações valiosas sobre o desempenho do acoplamento e ajudar a identificar áreas que precisam de atenção.
Outra prática errônea é não registrar as condições de operação e as manutenções realizadas. Manter um histórico detalhado sobre a instalação, manutenção e desempenho do acoplamento é vital para identificar padrões e prever problemas futuros. Sem essa documentação, as operações tornam-se mais difíceis de controlar e as causas de falhas podem se tornar desafiadoras de diagnosticar. Um sistema de registro deve ser implementado para auxiliar na melhoria contínua dos processos de manutenção.
Além disso, usar acoplamentos desgastados ou danificados é um erro que muitos profissionais cometem. Ignorar os sinais de desgaste e continuar utilizando um acoplamento comprometido pode levar a falhas mais sérias e interrupções inesperadas. Inspecionar regularmente os acoplamentos para verificar sinais de dano e substituí-los quando necessário é uma prática fundamental para garantir a continuidade das operações.
Por fim, um erro comum é não considerar o ambiente em que o acoplamento está operando. Condições adversas, como exposição a produtos químicos, umidade e temperaturas extremas, podem afetar o desempenho e a durabilidade do acoplamento. A escolha de um acoplamento que não seja adequado para essas condições pode levar a falhas. Portanto, é sempre importante avaliar o ambiente de operação ao selecionar um acoplamento e garantir que ele seja projetado para suportar essas condições.
Em conclusão, evitar erros comuns ao utilizar acoplamentos em redutores é fundamental para garantir operações eficientes e duradouras. A escolha correta do acoplamento, o alinhamento adequado dos eixos, a instalação e a manutenção apropriadas são aspectos cruciais que não devem ser negligenciados. Ao seguir as melhores práticas e implementar uma abordagem proativa para a manutenção, os operadores podem maximizar a eficiência e prolongar a vida útil de seus sistemas de transmissão de potência, garantindo operações contínuas e confiáveis.
Em suma, o acoplamento para redutor desempenha um papel crucial na eficiência e na eficácia de sistemas de transmissão de potência, sendo vital para o bom funcionamento de diversas aplicações industriais. A escolha do tipo correto de acoplamento, alinhada a práticas de instalação e manutenção adequadas, pode prevenir problemas operacionais significativos e prolongar a vida útil dos componentes envolvidos. Compreender as características específicas de cada acoplamento e como utilizá-las a seu favor garantirá não apenas um desempenho otimizado, mas também uma redução nos custos de operação e manutenção. Portanto, é imprescindível que profissionais e operadores adotem as melhores práticas discutidas neste artigo para assegurar que suas máquinas funcionem de forma eficiente e confiável, contribuindo assim para a produtividade e o sucesso dos negócios.